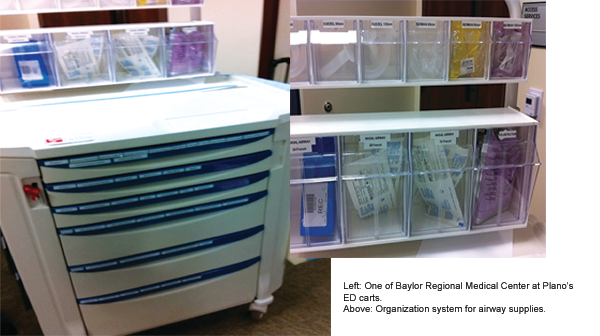
One of the most commonly observed features of the practice of emergency medicine is that workflow depends upon access to many and varying supplies. In any emergency department anywhere in the country right at this moment, myriad staff members (including physicians) can be observed scurrying around their departments, searching for and gathering the supplies necessary for treating the next patient. Most EDs tolerate a level of clutter and disorganization that most providers would not tolerate in their own homes.
Explore This Issue
ACEP Now: Vol 33 – No 06 – June 2014Kaizen is a Japanese workplace philosophy that means “improvement” and focuses on making small continual improvements that keep a business at the top of its field. The philosophy involves everyone in the organization, managers and leaders and workers alike, and urges them to make never-ending efforts for improvement. The foundation for Kaizen was laid after World War II when the country was attempting to rebuild infrastructure and rethink many systems. American leaders like W. Edwards Deming and Joseph Juran came to Japan to lecture and teach, and this lead to the Training Within Industry (TWI) programs, which subsequently gave way to Kaizen in the 1950s. The philosophy has been central to the cultures of companies like Toyota and Canon, where suggestions are regularly solicited from each employee, written down, shared, and implemented.
Kaizen has five key principles:
- There is heavy reliance on teamwork. Everyone’s opinion is valued and considered.
- Workers have a strong personal discipline, and morale must improve under Kaizen.
- Workers should be confident about offering suggestions, even when a system is already functioning adequately.
- Kaizen recognizes that there is always room for improvement.
- The system uses worker groups (also called quality circles) that meet and work together to both solve problems and come up with innovations.
This improvement model would seem particularly appropriate in the emergency department, which has many parallels to factory-floor processes. In emergency medicine, our product is urgent medical care, we work in teams to provide it, and many steps are involved in the delivery of that urgent care that have no intrinsic value to the patient (customer).
Another key feature of Kaizen has been termed the Five S of Kaizen. This is a method for organizing a workplace, especially a shared workplace like an emergency department.
- Seiri (Sort): Tidiness, keeping out only essential items out.
- Selton (Set in order): Orderliness, eliminating extra motion.
- Seiso (Shine): Cleanliness, keeping the workplace clean.
- Seiketsu (Standardize): Standardizing work practices.
- Shituke (Self-discipline): Sustaining and maintaining discipline and reviewing standards.
Kaizen in the ED
In a perfect example of Kaizen principles at work (though it was never dubbed as such), Alan Weier, MD, medical director for the emergency department at Baylor Regional Medical Center at Plano in Texas, spearheaded a project that involved the physician partners of 10 facilities within the Baylor Health Care System. The medical directors met for a strategic planning session in 2011, and one of their initiatives involved the standardization of equipment at all of their sites. They had three main areas of focus; two involved high-risk procedural equipment (airway and critical procedures), and a third focused on wound care.
The foundation for Kaizen was laid after World War II when the country was attempting to rebuild infrastructure and rethink many systems.
The ED council, which in effect served as a Kaizen quality circle, worked together to standardize the equipment for three important workflows in the ED: airway, critical procedures (chest tubes, invasive vascular access, lumbar puncture) and wound care (lacerations, incision and drainage). They developed master lists of equipment for each cart and purchased the carts and supplies at a reduced rate for all 10 campuses. These carts can be moved anywhere in the department, and this is in keeping with the new model for EDs in which any care can be rendered in any room. This standardization helped reduce clutter within the department and the need to run around the department in search of supplies for both high-acuity and high-frequency conditions within the department, standardized care. It also added discipline to the culture, and reduced costs.
The implementation phase for the change was just as important as the development of the carts. Dr. Weier and his team used staff meetings, education sessions, and checklists with photographs as part of the introduction of the carts, which took place at all sites. Continual feedback from providers ensured that the fine-tuning of the carts and their contents would be ongoing. The ED staff and physicians are so convinced that these standardized carts have improved care and increased efficiency and value that they are in the process of developing other carts for use throughout the system.
Dr. Weier and his team presented this work at the ED Innovations 2014 conference held in Las Vegas form February 19–21. It will be my pleasure to share with you more of the innovations that were showcased as posters at the conference. And apropos of the work done in Plano, I challenge you to return to your own department and “clean up your act!”
Dr. Welch is a practicing emergency physician with Utah Emergency Physicians and a research fellow at the Intermountain Institute for Health Care Delivery Research. She has written numerous articles and three books on ED quality, safety, and efficiency. She is a consultant with Quality Matters Consulting and her expertise is in ED operations.
Pages: 1 2 | Multi-Page
No Responses to “Japan’s Model for Workplace Organization Can Help Emergency Departments Improve Efficiency”